Home > Company News > Poker Production Process
Company News
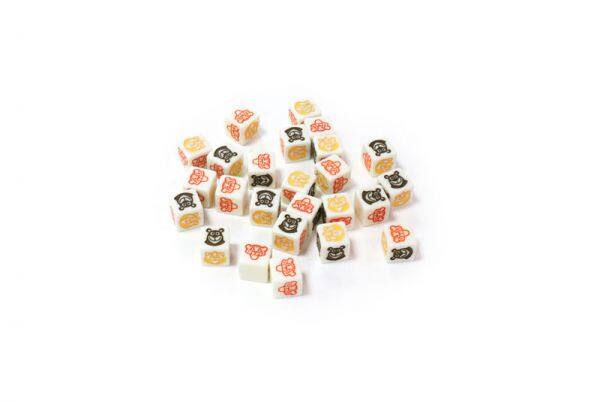
As a Cards Game Manufacturer, let's talk about the production process of playing cards today.
Design 54 cards to be arranged in 6x9 (54) or 7x8 (56) sizes. Because some cards need to print 55 or 56, the extra one or two are generally calendar or other advertising information. The paper is also cut to the corresponding size of 6x9 (54) or 7x8 (56).
2. Four-color front and back printing, as well as quality inspection. After the printing is completed, it is necessary to follow the ink absorbing characteristics of the paper, and the ink is sufficiently absorbed by the paper to proceed to the next process.
3. Front filling and drying.
4. Backfilling and drying. Filling is an important process in poker production. The so-called "filling" is a solution in which starch and other viscous chemical components are mixed and evenly applied to poker paper by rollers. This is because any paper will always have the symptoms of “bumpy†under the microscope, and poker needs to be very flat to ensure smoothness, and “filling†can make it smooth. Because there is moisture in the slurry, it needs to be dried at a medium to high temperature of 70 to 80 degrees.
5. Steel roller extrusion. Because the playing card paper is thicker, it consists of three or more layers. If it is not squeezed, there will be a case where the playing card has been playing for a long time and the front side is detached. Ten years ago, domestic poker also often showed a situation of positive back separation, but now this problem has been completely solved in large production plants. The squeezing effect is better after "filling".
6. Glazing. The glazing process refers to coating (or spraying, printing) a layer of colorless and transparent paint on the surface of the printed matter. After leveling, drying, calendering and curing, a thin and uniform transparent bright layer is formed on the surface of the printed matter to enhance The smoothness of the surface of the carrier and the finishing of the printed graphic. The glazing process has become an important means of finishing post-press finishing. It not only makes the poker pattern more beautiful, but more importantly, it is an important process to form a moderately smooth feel of poker. Of course, there is also a waterproof function. The glazing of poker should be determined according to the paper. The glare transition, the poker is too slippery, a stack of poker is easy to slip when stacked; if the glazing is insufficient, the poker is too sloppy, the playing cards are not easy to wash, and the cards are not inserted. (Note: Now, after four-color printing, it is varnished. The luminosity and slip of poker are related to the type of varnish used.)
7. Calendering and pressing fabric. Calendering refers to the process of hot pressing and cooling the finished product after drying the over-lit poker. The same as the calendering process of Plastic Dice, it is a deep processing process of glazing, which can make the glazing coated transparent coating more compact, smooth and high-gloss brightness ideal for the mirror layer effect, which can improve the grade of poker. Market Competitiveness. The cloth effect makes poker look more upscale and more handy. Many advertising poker customers want a cloth effect.
Plastic Dice
8. Perfume. Some customers need poker with a special scent, especially some food or cosmetic advertising poker. (added in the grout)
9. One die cutting and two die cutting. 54 cards are cut horizontally into 6 or 7 pieces by a die-cutting machine; then 9 or 8 pieces are cut longitudinally and automatically sorted to form a king at the top and a small king at the bottom. At the same time, quality inspection is carried out.
10. Separation. The so-called split card is to split the card cut into a single pair.
11. Poker core heat shrink packaging. The 54 cores of a pair of poker cards were heat-shrink wrapped with plastic paper by a packaging machine. The inner core is heat-shrinkable for easy packaging and moisture resistance. (Note: Generally, it is packaged with self-shrinking plastic film, heat shrinkage will deform the poker, uneven).
12.Printed poker box, there is also a PU Cards Box For Board Games on the market, which is more beautiful.
The above is the poker printing process. After reading it, I believe that you have a certain understanding of how to get the cards. In addition, if you want to know how to make other chess games, you can click on the link in the text and we will be happy to serve you.
-
Digital printing flannel polyester
-
0390116050 Original Used Machine Motor for KBA105 Hand Motor Offset Printing Machine Spare Parts Good Condition
-
L4.007.521 Bearing DS Tol.Gr.B For Heidelberg Sucker Bar Cpl XL Suction Device XL Operting Rod SX PM SM Printing Machine Part
-
0020.1922 0020.1909 Yellow Rubber Sucker Muller Martini 20.6mm OD x 6.4mm ID x 14.2mm H
-
C5.012.037 Gear Segment For Heidelberg CD 102 Brand New Accessories Printing Machine Part Original
-
M2.030.548F Adjusting Spindle For Heidelberg SM102 CX102 PM74 CD102 Printing Machine Parts
-
71.186.3631Llluminated Push Button Farblos Form 2 Separate Parts Set For Heidelberg Prinect Press Register Reader CD102 SM52
-
71.030.259 Printing Machinery Bearing For Heidelberg XL105 CX102 CD74 CD102 SM102 Heidelberg Brand New Original Accessories
-
68.110.1322 Reflex Sensor Front Lay Sensor RL2 For Heidelberg SM102 MO Printing Machine Parts Heidelberg Accessories
-
F2.016.279 Tooth Lock Washer For XL05 XL106 SX102 SM102 CX102 CD102 Heidelberg Offset Printing Machine Parts
-
Original New P0733680 Platten Plates Ersatzteil Gripper For Kba Printing Machine
-
L4.014.009 Roller Lever For Heidelberg SM102 SX102 CD102 CX102 Gripper Bar Cpl Printing Machine Parts
-
41.006.234 Leaf Spring For Heidelberg SM74 PM74 SX102 CD102 SM102 CX102 Blanket Cylinder Heidelberg OffsetPrinting Machine Parts
-
M2.184.1011 Pneumatic Cylinder D63.H18 Bosch For Heidelberg PM74 SM74 Printing Machine Part
-
91.008.080 Hickey Remover For Heidelberg Accessories SM102 CX102 CD102 Printmaster SO102 Printing Machine Part
-
71.010.048S Journal Box For Heidelberg SX 102 SM 102 CD 102 CX 102 Heidelberg Offset Printing Machine Parts
-
00.785.0063 Heidelberg Flat module ZSK2 Board 00.785.1156 Card 00.785.0406 Board 00.781.4117
-
M2.030.570F For Heidelberg SM74 Machine Rod Offset Printing Spare Parts SM74 Intermediate Roller
-
IJV4015004 Komori ink key motor original motor IJV-4015-D04 IJV401D004 IJV-4015-004 Komori Spare Parts
-
F2.028.450 Bar F2.028.451Guide MV.035.702 Sheet Steadier F2.028.454 Plate F2.028.453 Sheet Steadier C5.028.115 Sheet steadier
-
Roland 200 Machine Dampening Motor Z37M803451 Engine Z37M373399 Man Roland Spare Parts
-
L0847558 EC-Drive Ink Roller KBA Drive D230B004 For KBA Control Module
-
Red Anti-Marking Jacket SM102 For Heidelberg Offset Printing Machine Spare Parts 1035*770mm
-
KCS-59-75-S1-P Cylinder Kortis Tension-KCS Series Ultra Low Friction Cylinder KCS-59-75-S1-P Printing Machine Part